Oktober 18, 2024
Spritzguss
Fakuma
Sumitomo (SHI) Demag präsentiert neue Einspritzeinheit für die Medizintechnik
Eine neue Einspritzeinheit für den Bereich Medical stellt die Sumitomo (SHI) Demag Plastics Machinery GmbH, Schwaig, auf der Fakuma 2024 (Halle B1, Stand B1-1105) vor. Die kompakte IntElect mit 180 t Schließkraft ist mit einer 910-er-Spritzeinheit – der größten, die in dieser vollelektrischen Spritzgießmaschine untergebracht werden kann – ausgestattet. Das leistungsstarke Aggregat sorgt dafür, dass sie bei gleichbleibender Schließkraft höhere Präzisionsschussgewichte und einen höheren Einspritzdruck bewältigen kann. Gleichzeitig wird der Gesamtenergieverbrauch gesenkt.
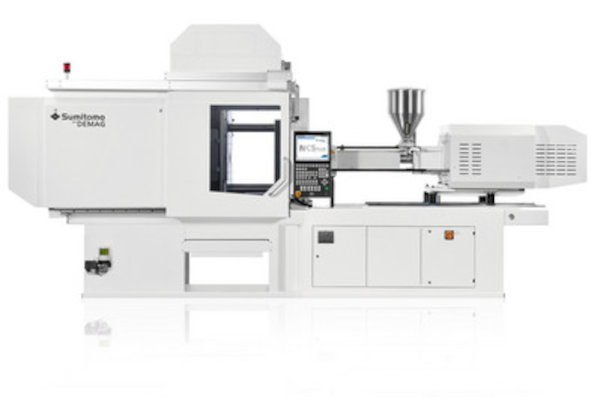
Bild: Sumitomo (SHI) Demag Plastics Machinery GmbH
„Wir erweitern damit das Anwendungsspektrum im Schließkraftbereich von 130 bis 180 Tonnen. Einer der Hauptvorteile der Wahl einer Maschine mit kleinerer Stellfläche, die größere Schussgewichte verarbeiten kann, sind die schnell zu realisierenden Energieeinsparungen“, sagt Andreas Montag, Business Development Director Medical und ergänzt: „Effizienz in der Medizintechnik setzt Präzision und Massenproduktion gleichermaßen voraus. Beides zusammen bildet die Grundlage für die Senkung der Gesundheitskosten für Patienten und medizinische Dienstleister.“
Verarbeitungsflexibilität und Produktionskapazität erhöht
Um diese flexible Kombination und die feine Verarbeitungssteuerung zu demonstrieren, werden auf dem Exponat mit einem 32-fach-Werkzeug alle 6,5 s Spritzenkolben aus einem nicht-porösen High Density Poly Ethylene (HDPE) mit einem Schussgewicht von 29 g gespritzt. Kunststoff-Verarbeiter haben die Möglichkeit, auch eine 50-mm-Schnecke hinzufügen, um größere Teile zu spritzen. Durch die Variabilität, schnell zwischen drei Schneckengrößen – 45, 55 und 60 mm, mit der Option, auch 50 mm hinzuzufügen – zu wechseln, wird sichergestellt, dass für jede medizinische Anwendung die optimale Schneckengröße gewählt wird. So werden Verarbeitungsflexibilität und Produktionskapazität weiter erhöht.
„Die Live-Demonstration wird zusammen mit elm-plastic realisiert, von denen auch das Werkzeug, das Kühlsystem und weitere Peripheriegeräte stammen“, erläutert Montag. „Diese hocheffiziente und kompakte Reinraum-Produktionszelle zeichnet sich durch Wiederholgenauigkeit und Sauberkeit aus. Sie wurde für hohe Geschwindigkeit und Präzision gebaut und ist so konzipiert, dass sie extrem enge Toleranzen bei medizinischen Anwendungen, die in hohen Stückzahlen produziert werden, auf die effizienteste Art und Weise handhaben kann, und gleichzeitig den Verarbeitern größte Flexibilität bezüglich der Bauteil-Größe bietet – von kleinen medizinischen Teilen bis hin zu größeren Komponenten.“
Produktionsvolumen pro Quadratmeter gesteigert
Anstatt die Entnahme der Komponenten zu automatisieren, wird bei diesem Exponat ein in der Produktionszelle installierter QS-Schalter verwendet. Wenn sich die Form öffnet, fallen die Spritzenkolben kaskadenförmig auf das Förderband, wobei Schlecht-Teile aussortiert und Gut-Teile gewogen und in ein von AM Plastics geliefertes, austauschbares Boxensystem gezählt werden. „Dies alles geschieht ohne Platzverlust. Die Produktivität wird erhöht, weil wir den Boden und die vertikale Fläche effizienter nutzen, um das Produktionsvolumen pro Quadratmeter zu steigern“, hebt der Experte hervor.
Ein weiteres Highlight präsentiert Hekuma (Halle A7, Stand A7-7202), anhand einer skalierbaren und flexiblen Reinraumkonfiguration für die Petrischalen-Produktion. Integraler Bestandteil dieses medizinischen Pakets ist eine IntElect2 100. Hekuma beschreibt die diesjährige Präsentation als „ein hervorragendes Beispiel für ein durchdachtes, automatisiertes, skalierbares und schlüsselfertiges System“. Es seid ideal für kleinere Produktionsserien geeignet und biete auch Massenherstellern von medizinischen Komponenten einen höheren Mehrwert.
Trotz Kosteneffizienz keine Kompromisse bei Qualitätsstandards
Die Zusammenarbeit mit dem asiatischen Werkzeugspezialisten Jestar Mold Tech zeigt darüber hinaus, wie hochwertige und innovative Lösungen kosteneffizient zusammenarbeiten können. Anstatt ein herkömmliches Etagenwerkzeug zur Herstellung von Petrischalen zu verwenden, liefert Jestar das 2+2-Seitenwerkzeug, das eine Zykluszeit von 7 s und eine hohe Produktionsleistung ermöglicht. Die Automation liefert Hekuma selbst: ein 6-Achs-Roboter entnimmt die Teile per Seitenentnahme.
Kosteneffizienz bedeutet dabei jedoch nicht, dass bei den Qualitätsstandards Kompromisse eingegangen werden müssen. Um die Einhaltung der Qualitätsmanagement- und Validierungsnormen ISO 13485 für Medizinprodukte zu gewährleisten, besitz die IntElect-Maschine feststehende Benutzerparameter. Dadurch wird sichergestellt, dass die Prozesse innerhalb bestimmter Bandbreiten gehalten werden und dass die Benutzer keine unerlaubten Änderungen an den Einstellungen für Druck, Temperatur, Durchfluss und Kühlung vornehmen können.
Quelle: Sumitomo (SHI) Demag Plastics Machinery GmbH